CNC machining, as the core mode of part production, involves several links, requiring all relevant departments and employees to pay great attention. From drawing design to project implementation and final product delivery, the entire production process must strictly follow the specifications. The production department needs to comprehensively consider the various factors affecting production efficiency and quality, such as the drawing of process drawings, part labeling errors, machining machine tools, tool selection, etc., to ensure a smooth production process.
When designing the parts processing program, you need to clarify the processing difficulties of different parts and select the appropriate processing method according to the characteristics of the parts. This not only reduces the waste of resources but also improves the overall production quality. This paper will elaborate on the following aspects, expecting to provide valuable reference for the research of experts in this field.
Difficulties in the machining of thin-walled combination parts
1. The characteristics of thin-walled parts
Thin-walled assembled parts have the advantages of being lightweight and resource-saving so they are widely used in many fields such as aerospace, automobile manufacturing, and precision machinery. However, their unique structural characteristics also make the processing process have many challenges. Compared with general parts, the processing of thin-walled parts is more complex, mainly reflected in the following aspects:
Susceptible to external factors: Thin-walled parts with low hardness are susceptible to deformation caused by factors such as pressure and temperature changes during the machining process. Deformation will not only affect the dimensional accuracy of the pat but also affect its performance in the mechanical equipment, which in turn may lead to equipment failure or performance degradation, resulting in economic losses.
Vibration in machining: In machine tool machining, due to the mutual collision between fixtures, tools, and other components, vibration is easy to generate, especially when cutting vigorously. Thin-walled parts are prone to deformation, which in turn affects the machining accuracy. Vibration not only affects the shape and accuracy of the part but may also increase the difficulty of machine tool maintenance and bring potential safety hazards.
Therefore, in the processing of thin-walled parts, in addition to considering conventional machining technology, but also pay attention to the impact of deformation, vibration, and other factors, to take corresponding countermeasures, to ensure the accuracy and stability of parts processing.
2. Tool selection
The role of the tool in the thin-walled combination of parts processing is critical, the choice of the right tool is directly related to the quality of parts processing and productivity. Tool selection requires comprehensive consideration of several factors:
Tool hardness and precision: thin-walled parts are susceptible to cutting forces and vibration, so the hardness of the tool should be moderate to ensure that the cutting process can provide sufficient strength, while not generating excessive vibration. Tools should have high accuracy to ensure dimensional control and surface finish during machining. Excessive vibration frequency may lead to machining errors, which in turn may affect the overall quality of the part.
Working environment and frequency: Depending on the machining environment, tool selection should be adjusted. For equipment that operates for long periods, it is recommended to choose tools with high hardness and moderate cost performance. On the one hand, this helps to reduce the need for frequent tool changes, ensuring production continuity and high efficiency; on the other hand, high-hardness tools are better able to resist prolonged cutting forces and wear, improving tool life.
Safety considerations: Long-term, high-load work will increase the possibility of tool wear. Choosing a wear-resistant tool with better toughness can effectively reduce the risk of wear or breakage, avoiding production accidents due to tool failure and protecting the work safety of employees.
Precautions during CNC machining
1. Drawing design
In the process of CNC machining, drawing design is the basis and important reference for parts production and processing. With the development of modern production technology, CNC machining technology has been widely used in various industries, requiring more accurate and standardized drawing design. The quality of drawing design directly affects the production efficiency and quality of parts, specific considerations include:
Accurate labeling and division: parts drawings should be clearly labeled with the specific requirements of each machining process and detailed division of each part of the parts. This will ensure that the production staff in the processing can accurately grasp the processing requirements of each part, to avoid production errors caused by deviations in understanding.
Avoid repeated processing: to avoid repeated processing in the production process, the drawing designer should ensure that the content of each processing link is unambiguous, and at the same time reasonably arrange the processing order to reduce the waste of resources and time.
Closely linked with the production process: the design process should take into account the actual situation of the production process, the content of the drawings, and the production process effectively docking. Through the fine management of drawings, can guarantee the work in an orderly manner, to improve the overall quality of parts processing.
2. Tool selection
Tool selection directly affects the parts processing accuracy and productivity. In the processing of thin-walled parts, the selection of tools is a key issue, specifically need to pay attention to the following aspects:
Tool characteristics and machining requirements: To choose the right tool first need to understand the characteristics of the parts. For example, for the form of simple parts, you can choose high-strength tools, such as cylindrical turning tools or diamond turning tools; for high-precision requirements of the parts, you should choose alloy tools to ensure dimensional accuracy and surface quality.
Working environment and equipment status: the selection of tools also needs to consider the working environment, equipment operation status, and other factors high-hardnesses tools can improve cutting efficiency and reduce tool wear but also need to pay attention to the durability of the tool, and wear resistance. According to the different states of the equipment, choose the right tool to improve productivity.
Safety and maintenance: The quality and selection of cutting tools are directly related to the safety of production personnel, especially those in the production line. Cutting tools should have good chip-breaking performance and brittleness resistance to minimize the damage of debris to the equipment. Regular inspection and maintenance of the tool to ensure that the tool is in good working condition, and to avoid production accidents caused by tool wear or breakage.
3. Clamping method
In CNC machining, the clamping method is essential to improve productivity. The correct clamping method can reduce errors in machining and improve machining accuracy and productivity. Related considerations include:
Optimize the clamping method: according to the specific characteristics of the machined parts, select the appropriate clamping method. For example, for thin-walled parts, reasonable clamping can reduce the deformation of the parts to avoid the accuracy problems caused by improper clamping.
Reduce the tool calibration time: through the reasonable design of the clamping, you can improve the workload of a single machining, and reduce the frequency of tool calibration, thereby saving time and improving productivity.
Equipment linkage: we should pay attention to the linkage between the equipment, especially the coordination of CNC machine tools and clamping equipment. Through the optimization of the clamping process, reduce the number of clamping, improve production efficiency, and ensure that each link is closely linked.
4. Tool setting and tool replacement
Tool setting and tool replacement an important parts of CNC machining, which have a direct impact on production efficiency and part quality. In the actual production process, tool setting, and tool replacement should be carried out the following requirements:
Professional skills and operating ability: the ability of professionals directly determines the efficiency of tool setting and the accuracy of replacement. Operators need regular skills training to improve the level of professionalism to ensure accurate tool setting and timely replacement of tools, to avoid the impact of production efficiency due to improper operation.
Timely tool replacement: Tool wear and breakage will lead to a decline in machining accuracy and even affect the normal operation of the equipment. Therefore, operators should regularly check the status of tools and replace worn tools in time to avoid production delays caused by tool failure.
Optimize the replacement process: Reasonable arrangement of the time and frequency of tool replacement can reduce the time required to change the tool and avoid unnecessary stoppages in the production process. To ensure that tool replacement does not affect the production schedule to ensure the continuity of the production process.
Thin-walled parts processing problems and treatment programs
Thin-walled parts are widely used in many fields due to their lightweight, small size, and compact structure. However, due to their thin wall thickness and poor rigidity, they are often prone to problems such as deformation and extension during machining, which in turn affects the size and accuracy of the parts. Therefore, the management of thin-walled parts processing has become the focus of CNC machining, and effective measures must be taken to ensure the quality of processing. The following are common problems and the corresponding treatment program:
1. Reasonable selection of workpiece structure and material
The deformation of thin-walled parts is closely related to the selection of materials and the structure of the parts. In the machining process, a reasonable choice of material and structure of the part is essential to prevent deformation.
Material properties and machining suitability: choose the appropriate hardness, plasticity,y, and stability of the material to ensure that the parts can withstand the stresses in the machining process without excessive deformation. For thin-walled parts, increasing the toughness and rigidity of the material can effectively reduce the risk of deformation.
Optimization of raw material ratios: According to the use of the environment and functional requirements of the parts, adjust the ratio of materials, optimize the quality of blanks, and ensure the compatibility of parts and materials and equipment, to improve the processing accuracy and quality of finished products.
2. Deformation due to pressure changes in the machining process
Thin-walled parts in the machining process are often due to external pressure or improper operation and deformation. Pressure-induced deformation is particularly prominent, especially for thin-walled parts, its rigidity is insufficient, easy to be affected by external forces.
Pressure control: In the machining process, the operator needs to pay special attention to the clamping force applied to the parts. The excessive clamping force of the fixture easily triggers deformation of the part, and even after machining, when the fixture is released, the part returns to its original shape, causing accuracy issues. Therefore, reasonable control of the clamping force is the key to avoid deformation.
Clamping process optimization: Reduce unnecessary external pressure, avoid over-clamping, and if necessary, reduce stress concentration by evenly distributing the clamping force. Ensure that you fix and stabilize the fixture during machining to prevent deformation caused by its instability.
3. Workpiece thermal deformation
Thermal deformation is a common problem for thin-walled parts in the machining process. Due to the poor rigidity of thin-walled parts, they are prone to dimensional changes at high temperatures, which in turn affects the machining accuracy.
Coolant and Cutting Temperature Control: The use of suitable coolant for cutting reduces the heat generated by the friction between the tool and the workpiece, and avoids thermal deformation of the workpiece due to high temperature. Coolant can effectively reduce the surface temperature of the workpiece to avoid thermal expansion caused by the large temperature difference.
High-efficiency cutting method: Selecting high-speed cutting technology can improve the efficiency of heat emanation during the cutting process and reduce heat accumulation. In addition, reducing the friction and heat generated during the cutting process also helps to reduce the risk of thermal deformation.
4. Deformation generated during the workpiece clamping process
Improper clamping is an important factor leading to the deformation of thin-walled parts. The clamping process’s unreasonable clamping method and fixture selection easily lead to parts producing stress concentration or deformation.
Reasonable selection of fixtures: select suitable fixtures for thin-walled parts, and ensure that the specifications and design of the fixtures are in line with the characteristics of the parts. For thin-walled parts, the use of too heavy or too complex fixtures, to avoid the fixture on the part producing excessive compression force.
Uniform distribution of clamping force: In the clamping process, one should try to choose the appropriate clamping position, and increase the contact area of the fixture to uniformly distribute the force and reduce the deformation caused by local pressure.
The use of elastic fixtures: you can use elastic fixtures or platens for fixing, these fixtures can effectively disperse the force, to avoid deformation caused by pressure concentration. For example, the use of elastic platens to distribute the clamping force and reduce damage to the part.
Support and Clamping Point Optimization: The support point of the fixture should be close to the machined surface to reduce the possibility of part deformation. Suitable clamping and support points can effectively reduce the deformation of the workpiece during machining.
5. Deformation of the workpiece during machining
During machining, changes in cutting force are another important factor leading to the o deformation of thin-walled parts. Excessive cutting force or improper cutting methods can easily lead to unnecessary deformation of the workpiece.
Tool sharpness and cutting method: To reduce the impact of cutting force on the workpiece, ensure that the tool remains sharp to prevent excessive cutting force caused by tool dullness. The use of high-speed cutting technology can effectively reduce the cutting force and reduce the deformation of the workpiece.
Cutting force control: Select appropriate cutting parameters, such as cutting speed, feed, and depth of cut, to control the size of the cutting force. Appropriate cutting parameters not only improve machining efficiency but also reduce the effect of cutting force on the deformation of thin-walled parts.
Chip cleaning: During machining, the cutting chips generated may accumulate between the tool and the workpiece, increasing friction and generating additional heat, which can lead to deformation of the workpiece. Therefore, timely cleaning of debris and keeping the machining area clean is an important measure to prevent deformation.
Methods to reduce the rate of deformation of thin-walled parts
The deformation of thin-walled parts is one of the main problems affecting machining accuracy and product quality. To effectively reduce the rate of deformation, it is necessary to use a variety of measures, combined with different machining stages and process requirements. The following are several effective methods to reduce the deformation rate of thin-walled parts:
1. Adopt different control methods by stages
The machining of thin-walled parts usually involves two stages: roughing and finishing. The roughing stage is prone to deformation of the part due to the large cutting volume and high clamping force; while in the finishing stage, the cutting volume is smaller, the clamping force is relatively low, and the deformation is smaller. Therefore, we can effectively reduce deformation by reasonably controlling machining in stages.
Roughing stage: in roughing, the parts of the larger margin, the clamping force needs to be larger, but at this time the deformation is also more obvious. Can take a larger depth of cut and higher cutting speed to reduce the cutting time, but to avoid excessive clamping force to avoid deformation.
Finishing Stage: In the finishing stage, the clamping force is lower, which can effectively avoid deformation caused by excessive fixture pressure. At this time, the main purpose is to correct the deformation caused by excessive cutting force during roughing, so it is necessary to use a smaller depth of cut and cutting speed to maintain the accuracy of the parts.
2. Combined with the actual needs of thin-walled workpiece processing to adjust the parameters
In the machining process of thin-walled parts, a reasonable selection of tools and machining parameters is the key to preventing deformation.
Select the appropriate tool holder: in the roughing process, the actual needs of the workpiece should be based on the selection of the appropriate tool holder, and ensure that the tool holder has sufficient rigidity. A suitable toholderrer can reduce vibration and avoid deformation during the machining process.
The trimming length of the cutting edge: when selecting a tool, the length of the trimming edge should not be too long, usually kept between 0.2-0.3mm. The sharpness of the cutting edge is also very important, to keep the tool sharp can reduce the cutting force and heat generation, thus effectively reducing the risk of deformation.
3. Utilizing axial clamping fixtures
Axial clamping is a type of fixture that reduces the rate of deformation on thin-walled parts. In contrast to traditional radial clamping, axial clamping distributes the clamping force along the axis of the workpiece, thus avoiding excessive concentration of stress in a particular area and reducing the incidence of deformation.
Clamping force distribution: The clamping force of axial clamping fixtures can be evenly distributed to avoid localized deformation of the workpiece due to uneven clamping of the fixture.
Improvement of fixing stability: axial clamping fixtures can provide strong fixing force during machining, effectively preventing the deformation of thin-walled parts due to their rigidity.
4. Expand the fixture contact area
Increasing the contact area of the fixture is another effective way to reduce the deformation of thin-walled parts. By increasing the area of contact between the fixture and the workpiece, the clamping force can be effectively dispersed, thus reducing the risk of deformation.
Use soft jaws or slit sleeves: Specially designed soft jaws or slit sleeves can be used to increase the fixture contact area during machining. These fixtures are effective in spreading the clamping forces and avoiding excessive pressure on the part, thus reducing the risk of deformation.
Dispersion of clamping force: Increasing the contact area of the fixture allows the clamping force to be distributed more evenly over the surface of the workpiece, thus avoiding localized over-pressure leading to deformation.
Actual case of thin-walled parts machining
1. Process flow analysis
Take the thin-walled combination part shown in Figure 1 as an example, the part is made of stainless steel, which has high machining requirements, especially in terms of precision control. Due to the material properties of stainless steel, the machining process faces several challenges, such as:
High cutting temperature: the high thermal conductivity of stainless steel makes the cutting temperature high, which easily leads to increased tool wear.
Difficulty in machining: Due to the high hardness of the material, the cutting force during machining is high, which can easily cause deformation.
The hardening phenomenon is serious: in the cutting process, the surface of the part is prone to hardening, increasing the difficulty of subsequent processing.
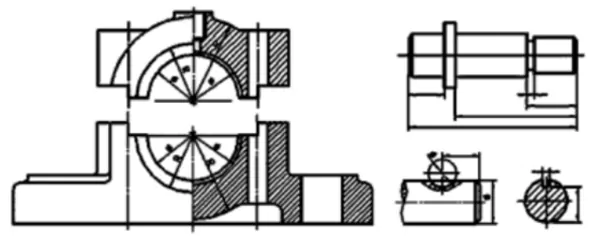
Figure 1 thin-walled combination parts
Figure 2 shows the unreasonable aspects of the machining process of the part. Compared with Figure 1, the main problem occurs in the inconsistency of the hole size, resulting in differences in the overall proportion of the part. This inconsistency in aperture size:
Poor diaphragm fit: the variation in aperture size leads to inconsistent fit of the diaphragm to the part, increasing friction.
Safety Hazard: Excessive friction may cause the blade to fly out, and in severe cases may even cause personal injury.
Improvement measures:
Strictlybyh the proportion of the production: in the process of processing, to ensure the consistency of the proportion of the hole diameter and the parts, to avoid the adverse effects of changes in the diameter of the hole.
Choose a suitable cutting method: Combine the material characteristics, choose a suitable cutting method, and control the cutting temperature and cutting force to reduce the hardening phenomenon.
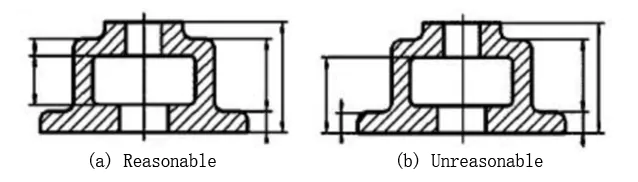
Fig. 2 Schematic diagram of the comparison between reasonable and unreasonable in the production process
2. Machining process
The machining of parts usually includes five key processes:
Cutting face: Ensure that the cutting length is appropriate, and initially remove part of the material.
Roughing: Remove most of the excess material, leaving enough margin for finishing.
Finishing: Fine-tuning of the part dimensions, improving surface quality, and ensuring part accuracy.
Rough Turning Bore: Handle the roughing part of the bore to prepare for finishing.
Finetuning of bore: Carry out the finishing of the bore to ensure that the bore diameter and surface finish meet the requirements.
In these processes, we need to adjust some important machining parameters, such as:
Tool number: T01/S800/F60/1.5
Spindle speed: T01/S800/F60/1.0
Feed speed: T02/S1000/F40/0.2
Backdraft: T03/S600/F60/1.0
Tool selection:
Rough turning external round: use the external round cutter, the insert material is YG8 alloy, and the control port angle is 90 degrees.
Precision turning outer circle: use YW1 alloy insert, the port is the same as rough turning.
Turning internal hole: use a white steel cutter (W18Cr4V) to process Φ14 internal hole, because the hole diameter is small.
In actual processing, the staff should adjust the process and tool selection according to the specific situation to ensure the processing effect.
Conclusion
Thin-walled combination parts have a wide range of applications, but in actual processing, technicians must improve their skill level and take reasonable measures to avoid deformation during processing. This paper analyzes the difficulties in the processing of thin-walled combination parts, and puts forward targeted solutions, focusing on the key issues in the processing process. By optimizing the machining process and applying reasonable technical means, we can effectively reduce the risk of deformation and improve the machining accuracy, ensuring the machining quality of the parts.