Five-axis linkage CNC machine tools, known as the “industrial mother machine,” play a vital role in advancing national industrial strategies and accelerating manufacturing development. Their high precision and efficiency make them essential in fields like aerospace, marine, military, and medical equipment.

Advantages of five-axis linkage CNC machine tools
1. Ability to process complex shapes
Five-axis CNC machine tools can process complex workpiece shapes, such as impellers, blades, and integral leaf disks in the aerospace field, which three-axis machines cannot handle. During machining, 5-axis machines can effectively avoid tool interference, use shorter tools to improve system rigidity, reduce the number of tools, and avoid the need for specialized tools.
2. Reduce the number of clamping and fixture use
Compared with three-axis CNC machine tools, five-axis CNC machine tools can significantly reduce the number of clamping and datum conversions, thereby reducing the use of fixtures. This efficient machining method not only improves machining efficiency but also improves machining accuracy.
3. Highly flexible and highly integrated
Five-axis linkage CNC machine tools have a high degree of flexibility and integration, and can comprehensively solve the aerospace, automotive, and other fields in the new product development process faced by the complex parts machining accuracy and cycle time problems. This ability greatly shortens the development cycle and improves the success rate of new products.
The basic structure of five-axis linked CNC machine tools
The basic structure of a five-axis CNC machine tool mainly consists of a “3+2” configuration, which includes three linear axes of motion (X, Y, Z) and two rotary axes (A, B, C) around these axes. Based on the different combinations of rotary axes, we can categorize five-axis machine tools into the following types:
1. Double rotary table structure of five-axis CNC machine tools
The 5-axis CNC machine tool with a double rotary table structure adopts the design of the 4-axis + C-axis, which makes it great flexibility and high efficiency in machining.
Structure features:
4-axis design: The bed supports the worktable, allowing it to rotate around the X-axis, which defines the 4-axis. Its working range is generally 30° to 120°, which can adapt to a variety of machining needs.
C-axis rotary: the rotary table located in the center of the table can rotate around the Z-axis, and the C-axis has the ability to rotate 360° in all directions. This feature makes the machine capable of machining multiple surfaces of the workpiece.
The combination of the 4-axis and C-axis allows for fully machining workpieces fixed to the table. Using a vertical spindle, enables the machining of the other five faces with high precision, in addition to the bottom face, thereby improving machining efficiency and flexibility.
The five-axis machine tool uses a double rotary table structure, which is widely employed to manufacture aerospace and automotive parts, as well as complex molds. It has become an important piece of equipment in high-end manufacturing due to its ability to efficiently process complex-shaped parts.
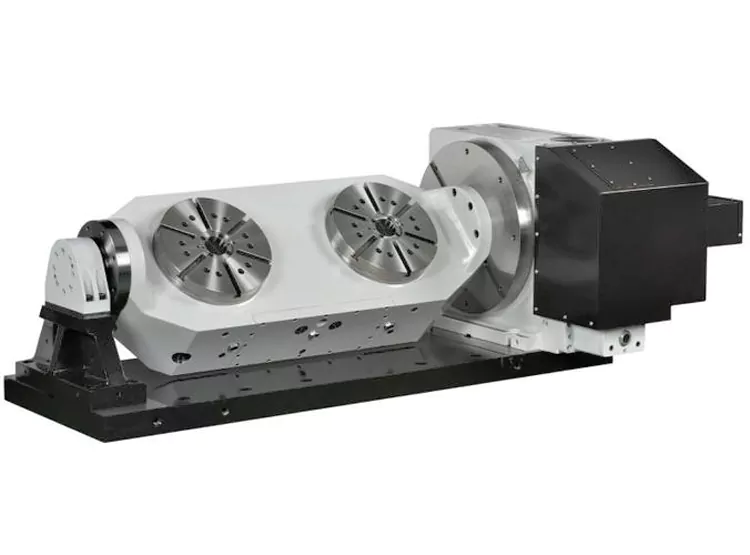
2.5-axis CNC machine tool with rotary table and pendulum head structure
In the rotary table and pendulum head structure of five-axis linkage machine tools, the rotary table or pendulum head can use the A-axis, B-axis, or C-axis.This flexible combination allows the machine to adapt to a variety of processing objects and needs.
Advantages:
Flexible machining: Since the spindle can be machined at multiple angles, the machine tool is able to create more complex shapes and curved surfaces to meet the production requirements of different parts.
Extended table: By increasing the table area, this structure can effectively support the machining of large and complex workpieces, improving machining capacity and efficiency.
Improvement of efficiency: It reduces the number of workpiece clamping and optimizes the machining process, thus improving the overall machining efficiency and accuracy.
The 5-axis machine tool with a rotary table plus pendulum head structure is widely used in aerospace, automobile manufacturing, and mold processing industries, making it an important piece of equipment in modern manufacturing due to its significant advantages in high-precision and high-efficiency machining.
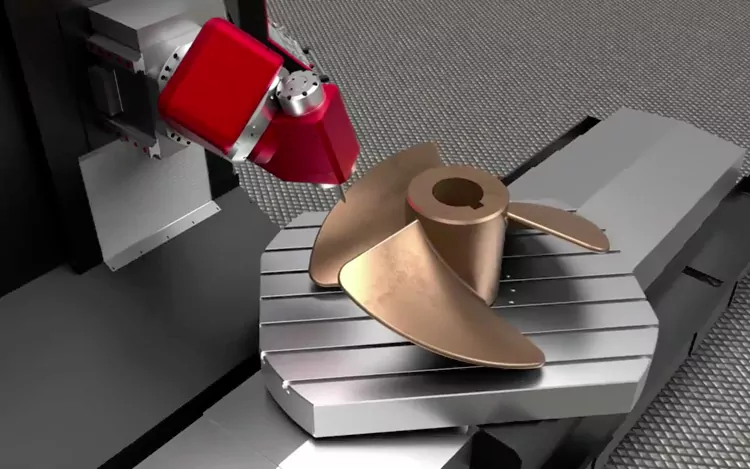
3. Five-axis CNC machine tool with double pendulum head structure
The double pendulum head structure of the five-axis linkage CNC machine tool design has a unique advantage, suitable for handling large and complex workpieces.
Structure features:
Pendulum head design: The electric spindle with a loose pulling tool structure equips the pendulum head of this machine tool, ensuring its flexibility and stability in the machining process. As the size of the double pendulum head generally ranges from 400mm to 500mm, it can meet various machining requirements.
Machining range: The double pendulum head structure usually adopts a gantry or moving beam gantry layout, with the width of the gantry generally ranging from 2000mm to 3000mm. This design allows the machine to handle larger and more complex workpieces.
“Zero-drive” technology: Currently, most of the advanced double pendulum head 5-axis machine tools use torque motors with “zero-drive” technology. The application of this technology effectively improves the rigidity and accuracy of the rotary axis and reduces errors in the transmission chain.
The five-axis machine tool with a double pendulum head structure enables high-precision machining at multiple angles and directions. Aerospace, automotive manufacturing, mold processing, and other fields widely use it to meet the production needs of highly complex parts, thereby enhancing overall production efficiency and processing quality.
Five-axis linkage CNC machine tool research status at home and abroad
1. Five-axis linkage CNC machine tool research status abroad
Currently, the research and development of five-axis linkage CNC machine tools are primarily driven by developed countries, particularly in Europe, the United States, and Japan, which represent the highest level of advancement in this field. As technology continues to progress and the demand for high-grade CNC machine tools rises, foreign manufacturers are increasingly focusing on making these machines faster, more precise, intelligent, reliable, and environmentally friendly.
Germany’s Innovations: SycoTec and Zimmermann
SycoTec 4015 DC-R-HSK63 High-Speed Precision Spindle
SycoTec has introduced the 4015 DC-R-HSK63 high-speed precision spindle, designed for five-axis CNC machining centers. This advanced spindle has significantly expanded the machine tool’s speed range, from 0–24,000 r/min to an impressive 0–100,000 r/min, enabling ultra-high-speed precision machining. Additionally, the standard HSK-63 tool holders ensure quick, frictionless tool changes, reducing downtime and boosting production efficiency.
Zimmermann’s High-End CNC Machines with Curved Guideway
Zimmermann’s five-axis CNC machines feature the M3ABC with a high-end, curved guideway, incorporating three different rotary coordinate heads—4, B, and C. This design offers excellent rigidity and a compact structure. The C-axis’s unrestricted rotation enhances machining accuracy, even during complex processes.
France’s Multifunctional Machining Centers: SOMAB
DIAM Five-Axis Machining Centers
The French company SOMAB manufactures the DIAM series five-axis machining centers, which integrate turning, milling, boring, drilling, gear processing, and crankshaft machining. These multifunctional centers significantly boost machining efficiency and accuracy, making them highly versatile for a range of applications.
U.S. Technological Advancements: Hurco and Haas
Hurco’s I series five-axis machining centers utilize an integrated electric spindle with high-precision ceramic bearings, allowing continuous rotation of the machining table without angle restrictions. This feature minimizes beat time and maximizes tool feed, ensuring superior performance in complex part machining.
The VF-6TR series by Haas provides fully synchronized 5-axis motion, allowing the workpiece to be positioned at nearly any angle for machining. This enhances the flexibility and efficiency of machining, particularly for intricate parts and complex geometries.
Japan’s Precision Engineering: YASDA and Mazak
The YBM Vi40 ultra-precision CNC machine tool, developed by YASDA Kogyo Co., Ltd., features a rigid integrated bridge structure for high-precision machining, particularly in die and mold manufacturing. Its stable performance ensures exceptional surface quality and fine machining accuracy.
Mazak’s VARIAXISi series CNC machining centers can process complex curved surfaces on large, heavy parts in a single clamping. This Done-in-One concept shortens processing time and improves accuracy by performing all machining processes—roughing, finishing, and even final assembly—on a single machine.
South Korea’s Cutting-Edge Technology: Hyundai Wia
Hyundai Wia’s XF6300 series features a high-speed, high-precision five-axis vertical machining center ideal for advanced mold and high-precision machining. It incorporates a 15,000 r/min spindle paired with a high-precision spindle, reducing vibration and achieving micron-grade precision.
Italy’s FIDIA: High-Speed Milling for Automotive and Mold Industries
FIDIA’s five-axis vertical machining centers are equipped with spindles that can reach up to 24,000 r/min, combined with an AC oscillating head. These machines are primarily used for high-speed milling in automotive and plastic mold industries, as well as for components like bumpers, lights, and interior molds.
2. Five-axis linkage CNC machine tool domestic research status quo
China’s Development in Five-Axis Linkage CNC Machine Tools
In recent years, China has made significant strides in CNC technology. However, due to its relatively weak industrial foundation and short history of CNC machine tool industrialization, there remains a technological gap, particularly in high-end five-axis CNC machine tools. Compared to international standards, China lags in the reliability, efficiency, precision retention, and intelligence of its five-axis systems.
National Support and Industry Collaboration
Under the “Made in China 2025” initiative, China has prioritized high-end CNC machine tools and basic manufacturing equipment. This strategic focus has led to substantial progress in the R&D of five-axis CNC machine tools, moving from trials to mass production. The combined efforts of national policies, enterprises, and research institutions have spurred innovation.
Key Developments by Leading Companies
Wuhan Huazhong CNC
Huazhong CNC has developed an 8-type five-axis CNC system with independent intellectual property rights. This system is compatible with various rotary table CNC machine tools, significantly enhancing processing efficiency. It powers high-grade five-axis machine tools, such as the AC pendulum head 5-axis gantry machining center and the BC pendulum head 5-axis vertical machining center.
KD CNC
KD CNC’s DMC50 dual five-axis vertical machining center adopts a modular design, integrating turning, ultrasonic machining, and grinding modules. It supports multi-process machining in a single clamping, boosting precision and efficiency, particularly for industries like aerospace, automotive, and semiconductor manufacturing.
Shenyang Machine Tool
Shenyang Machine Tool broke foreign monopolies in five-axis CNC technology with its 2010 launch of the VMC25100u vertical five-axis machining center for titanium alloy aerospace parts. It later developed the first high-speed five-axis machining center for the high-speed rail industry, overcoming challenges in lightweight design and high-precision machining.
Jinan No. 2 Machine Tool
This company showcased its XHSV2525Ax40 high-speed five-axis machining center, which integrates an AC-axis dual-pendulum CNC milling head. It is capable of high-precision, high-efficiency machining for complex aerospace and automotive parts.
Advanced R&D Projects and Collaborations
Beijing Machine Tool Research Institute
At the 17th China International Machine Tool Exhibition, the Institute presented the μ1000/5ST-400V precision five-axis machining center. This machine excels at high-efficiency, high-accuracy machining of complex components for national key industries.
Shanghai Jiao Tong University & TOP CNC
They developed dual five-axis mirror milling technology, enabling high-precision machining of aerospace components like aircraft skins and rocket surfaces. This innovation addresses key challenges in closed-loop control and precision for large-scale machining.
Tsinghua University and Nanjing University of Aeronautics and Astronautics
These universities collaborated on R&D projects to improve the accuracy of five-axis CNC machine tools. Their research focused on calibration technology, online measurement, and speed control to optimize the machining of complex aerospace components.
Conclusion: Progress in High-End CNC Machine Tools
China has made remarkable progress in the research and development of high-end five-axis CNC machine tools. With continued collaboration between universities, enterprises, and government initiatives, China is closing the gap with international standards and making significant strides toward self-reliance in this critical field.
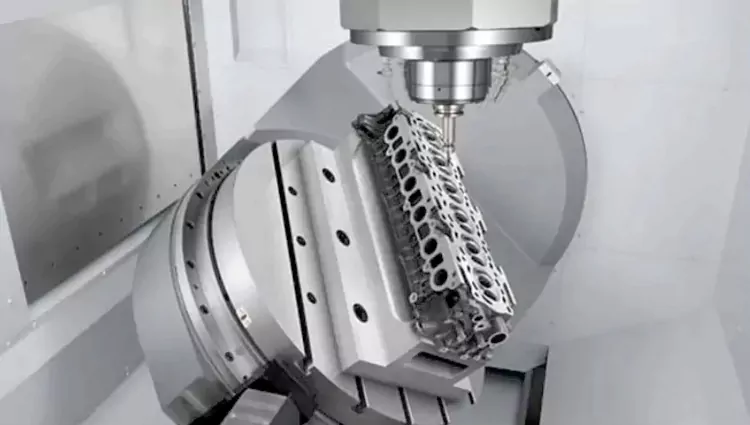
The development trend and future outlook of five-axis linkage CNC machine tools
1. Development trend
From the above domestic and foreign five-axis linkage CNC machine tool research status can be seen, today’s five-axis linkage CNC machine tool development trend is.
1) High speed
With the continuous progress of machine tool technology, five-axis linked high-speed CNC machine tools have achieved significant breakthroughs in high speed in many aspects. These technological advances include:
High-speed feed mechanism: the new feed mechanism allows CNC machine tools to achieve higher feed speeds, which directly improves machining efficiency. Currently, the actual speed of fast-moving parts has reached 120m/min, which greatly reduces machining time.
High-speed electric spindle: modern CNC machine tools are equipped with electric spindles, whose actual speed has reached 100000r/min. The realization of this high speed makes the machine tool able to cut a variety of materials more efficiently, to meet the processing needs of complex parts.
Cutting Feed Speed Increase: The cutting feed speed of the machine system has been increased to 60m/min, which effectively improves the efficiency of parts machining and reduces auxiliary time. This means that more machining tasks can be accomplished in a shorter period, thus increasing overall productivity.
These high-speed advances not only reduce part machining cycle times but also increase productivity, providing strong support for manufacturing competitiveness. Through continuous innovation and technological upgrades, five-axis linked CNC machine tools are developing in the direction of greater efficiency and precision.
2) Precision
Five-axis linkage CNC machine tools have significant advantages in processing precision, with the progress of computer-aided manufacturing (CAM) system, its precision has reached the micron level. This development mainly reflects the following aspects:
High-precision machining: The design and control system of five-axis machine tools enable them to effectively ensure dimensional and shape accuracy when machining high-precision parts. By precisely controlling the motion of each axis, the machine can accurately execute complex machining paths and reduce errors.
Reduces machining errors: High-precision positioning and cutting control help avoid the accumulation of errors during machining, resulting in a more consistent quality of the final product. This is especially important for industries such as aerospace and medical devices, which require a high degree of precision.
Integrated Machining Process: The application of CAM systems makes the entire process from design to machining more efficient and precise. Designers can directly simulate and optimize the software to ensure they achieve the expected high-precision results during the production process.
Precision machining not only improves the quality of products but also enhances the competitiveness of enterprises in the market. This trend makes five-axis linkage CNC machine tools in the field of high-end manufacturing play an increasingly important role in promoting the overall progress of the industry.
3) Composite
The composite technology of five-axis linkage CNC machine tools continues to develop, adapting to the processing needs of polyhedral and curved surface parts, and promoting the integration of multiple processing procedures. Mainly reflected in the following aspects:
Multi-functional machining centers: new five-axis machine tools, such as five-axis turning and milling composite machining centers, boring and milling composite machining centers, and milling, boring, drilling, and turning composite machining centers, are capable of simultaneous milling, drilling, tapping, and other machining operations. This composite machining capability makes it possible to complete multiple processes on complex parts in a single clamping, significantly improving machining efficiency.
Processing Efficiency Improvement: Through composite technology, manufacturers dramatically reduce the cycle time of complex parts during machining. The simultaneous execution of multiple processes reduces the number of workpiece clamping and changeover times, thus speeding up the overall production process.
Flexibility and Precision: The flexibility of the composite machining center allows the machine to respond to a wide range of machining requirements, while the highly integrated design ensures machining precision to meet the modern manufacturing industry’s demand for high-quality products.
Composite technology not only improves productivity but also optimizes the machining process, reducing the possibility of manual intervention and error, and providing manufacturing companies with greater flexibility and competitiveness. This trend makes five-axis linkage CNC machine tools in modern manufacturing more and more important.
4) Intelligent
As advanced technologies such as artificial intelligence, big data, and the Internet of Things continue to develop, five-axis linked CNC machine tools are rapidly advancing toward intelligence, primarily reflected in the following aspects:
Intelligent Optimization and Selection of Processing Parameters: Through data analysis and algorithms, CNC machine tools are able to optimize processing parameters in real-time, such as cutting speed, feed rate, etc., in order to adapt to different materials and machining conditions, thereby improving processing efficiency and quality.
Adaptive Control: Intelligent technology enables the machine tool to automatically adjust operating parameters during machining to cope with environmental changes or differences in material properties, achieving higher machining stability and consistency.
Intelligent Fault Diagnosis and Self-Repair: CNC machine tools can monitor their status, carry out intelligent fault self-diagnosis, discover potential problems in time, and carry out self-repair, thus reducing downtime and improving productivity.
Fault playback and simulation: The intelligent system can record fault information during machining and perform playback and simulation analysis to provide data support for subsequent optimization, thus improving the reliability of the machine tool.
Intelligent AC Servo Drive: The new generation of servo drive supports intelligent AC, which is capable of realizing efficient motion control and precise dynamic response, further enhancing machining accuracy and speed.
Intelligent development not only improves the automation level of five-axis linkage CNC machine tools but also significantly improves their productivity and machining quality, providing strong support for the intelligent transformation of the manufacturing industry. This trend will enable enterprises to maintain a leading position in the fierce market competition and promote the entire industry to a higher level of development.
5) Flexibility
Five-axis linkage CNC machine tools in the processing of complex surfaces and diverse workpieces show strong adaptability, mainly reflected in the following aspects:
Multi-surface machining in one clamping: five-axis linkage CNC machine tools are able to complete the machining of multiple surfaces and different angles in one clamping, which reduces the steps of traditional CNC machine tools that require multiple clamping and turning of parts, thus improving the machining efficiency and accuracy.
Adaptation to diversified processing needs: With the diversification of manufacturing needs, 5-axis machine tools can flexibly cope with different types and specifications of workpieces and are suitable for the processing of complex parts in aerospace, automotive, mold, and die industries to meet the requirements of high precision and high complexity.
System Flexibility: Modern CNC machine tools are developing towards modularization and systematization, adopting flexible manufacturing units and production system configurations that allow the machine tools to quickly adjust and reorganize according to production demands, enabling them to adapt to different production tasks.
Intelligent Flexible Management: Combined with intelligent manufacturing technology, five-axis machine tools can monitor and adjust the machining process in real time, optimize the allocation of resources, and achieve a rapid response to the changing market demand.
The development of flexibilization enables five-axis CNC machine tools to have higher adaptability and efficiency in the production process, reduces manufacturing costs, shortens the delivery cycle, and further promotes the feasibility of personalization and small-batch production. This trend will help companies stay competitive in the rapidly changing market environment.
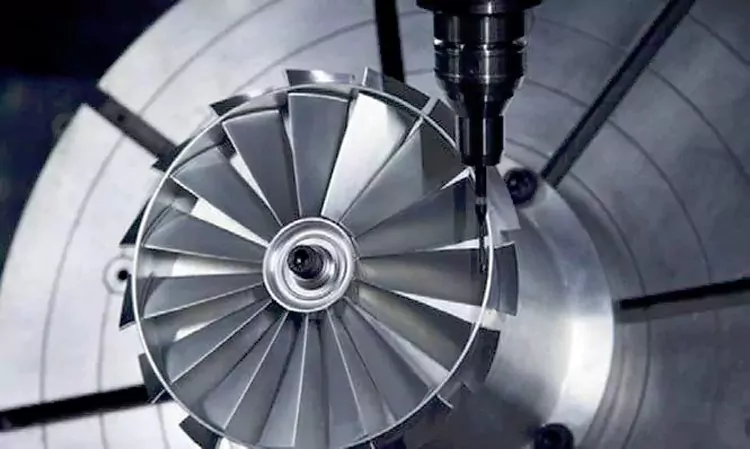
2. Future Outlook
The future development of five-axis linkage CNC machine tools will continue to move in the direction of high-speed, high-precision, composite, intelligent, and flexible. However, compared with Europe, America Japan, and other developed countries, there is still a gap between China’s five-axis linkage CNC machine tool technology and industrial development. To narrow this gap, we recommend the following measures:
1)Build a collaborative innovation system
Vigorously build an enterprise-oriented collaborative innovation system of industry, academia, research, and utilization to promote the core technology of high-end CNC machine tools. This will provide technical support for the strong and complementary chain of the industrial chain, and enhance the independent and controllable ability of China’s five-axis linked CNC machine tool industry chain.
2)Emphasize basic common technology research
The national R&D department should increase the investment in basic common technology research in the field of high-end CNC machine tool equipment manufacturing, build a national key laboratory for five-axis linkage high-end CNC machine tools, improve the common technology innovation system, and promote technological breakthroughs.
3)Cultivate high-end technical talents
Taking the release of “Made in China 2025” as an opportunity, focusing on the strategic needs of the national manufacturing power, dynamically adjusting the subject settings of higher education, and strengthening engineering education and science education. In particular, we should focus on the cultivation of top-notch talents in high-end CNC technology to provide a solid talent guarantee for the attack of key core technologies.
Conclusion
Five-axis linkage CNC machine tools play a vital role in the modern manufacturing industry, especially in aerospace, automotive medical equipment, and other fields, its high precision and high-efficiency characteristics make them key processing equipment. By machining complex shapes, reducing the number of fixtures, and providing high flexibility and integration, 5-axis machines significantly improve productivity and accuracy.
With the advancement of technology, five-axis machine tools are developing towards high-speed, intelligent, and green, gradually narrowing the gap with the international advanced level. Domestic research institutions and enterprises are also actively promoting independent innovation, overcoming key technologies, and gradually realizing the transition from R&D to mass production. Looking ahead, five-axis CNC machine tools will play a greater role in improving machining quality, efficiency and meet the demand for complex machining, and help the transformation and upgrading of the national manufacturing industry and competitiveness.